Our Technology
To reduce Energy Consumption and Enhance Efficiency



Valves solution for power plant
ZERO LEAKGE METAL SEATED BALL VALVE
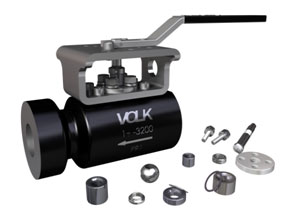
Most solutions for improving the efficiency of existing power plants
are focused on the boilers and steam turbines while ignoring the significant
leakage from valves.
The severe service valves operating at 3200 psi to 3800 psi and 1004
deg F to 1250 deg F are critical to performance and efficiency and
a small leak in these valves propogates to larger leaks with service
life. This means that super critical steam leaks from the valve instead
of being passed through to the steam turbines
resulting in less electrical power being produced by the generators.
This significantly reduces plant efficiency and causes an imbalance
of the thermal system. Actual plant studies have shown that steam
leakage from the valves reduces the efficiency of the generators by
2%-3%.
Volk Flow Controls, Inc zero leakage severe service metal seated ball
valves are proven in service as the most economic and practical solution
for valve leakage problems.
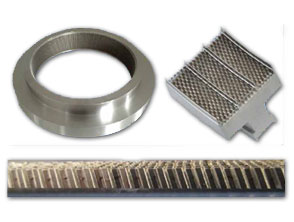
Honeycomb seals have, for many years, been widely used in aircraft engines
and gas turbines with great advantages in safety and efficiency compared
to the comb seal.
The honeycomb seal was designed and first applied in the U.S.A. In China,
turbine seals were applied in power plants over 20 years ago------first
in the shaft end of steam turbines and later in the shaft end, baffle
plate, blade tip, etc. of the steam turbine. A case study performed by
Shanghai Turbine Corporation Limited and Thermal Testing Research Institutions
showed that the efficiency of generators using honeycomb seals is enhanced
by 1%-3%.
The following table shows the benefits that honeycomb seals bring to a
300 MW generator:
The cylinder
efficiency of the whole generator is improved by at least 3.9%.
The Turbo Star seals developed by Beijing LAD Electric and Power Technology
Co., Ltd. improved the design of the honeycomb seal in which the honeycomb
is inclined at β° angle and welded to the base, resulting in improved
efficiency.
In addition, by using honeycomb seals, the cost of refurbishing generators
is greatly reduced.
Honeycomb seals can be easily installed during outages or when the generator
is scheduled for maintenance, thus saving considerable energy and at the
same time reducing the emission.
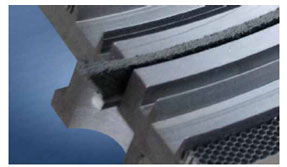
The majority of air preheaters use a fixed seal. The air leakage rate
of air preheaters is about 5% to 7% during one year’s operation rising
to 6% to 12% after a year’s operation subject to different management
and designs, which directly affect the operating efficiency.
For the power plant boiler, when the air leakage factor of the boiler
cavity increases 0.1-0.2, the exhaust gas temperature will increase by
35 degF to 50 degF and the boiler efficiency will decrease by 0.2~0.5%.
Assuming that the boiler efficiency is improved by 1%, then:
For example,
if the smoke exhaust of the boiler decreases from 7.0% to 6.0%, the air
leakage factor decreases by 0.1%, and the boiler efficiency increases
by 0.25%. Coal consumption for a 300 MW generator will be saved:
2.0 g/ kW.h × 0.25 = 0.5 g/ kW.h
The new re-designed brush seals air preheaters can maintain the air leakage
rate below 5%, thus improving the boiler efficiency by about 1%. The new
re-designed brush seals efficiently solves the serious air leakage problem.
and reduces the emissions of NOX and SOX.
The
refurbishing of steam turbines can enhance the efficiency of the generators
by 10%. The majority of generators (≦ 300 MW) are refurbished in the flow
process.
Refurbish a 300 MW generator for example:
Heat consumption is reduced by 300 kJ/kW. h and coal consumption is reduced
by 10.2 g/kW.h.
If the generator runs 5000 hours per year, then 15300 tons of coal will
be saved. Cost savings:
15300 × $138 =$2,111,400 (USD) based on a coal price of $138/ton
Suppose 2620 kg CO2 , 8.5kg SO2 and 7.4kg Nitrogen Oxides will be generated
combusting 1 ton coal, then the reduced emission by refurbishing:
CO2: 2620 ×15300= 40086 (tons)
SO2: 8.5 ×15300= 130 (tons)
Nitrogen Oxides: 7.4 ×15300= 113 (tons)
GASIFICATION SMALL OIL GUN IGNITION AND STABLE COMBUSTION TECHNIQUE
Feng’s environmental protection includes “Energy Saving High Efficient De-dust Technology”, “Energy Balanced FGD Technology”, “Energy Saving High Efficient Whole Day SCR Technology” and “Safe, Energy Saving, Lifetime Extending Technology of SCR Catalyst”, “Anti-Blocking and Anti-Corrosion Technology for Air Preheater”.
I. Illustration of Environmental Protection
a) Energy Saving High Efficient Series of De-dust Technology
The total flue gas has been greatly declined by reducing the leakage of
the air preheater, applying high efficient lower oxygen combustion technology
and improving the unit efficiency.
Modify the power supply unit of the electric precipitator by applying
high frequency power technology. Change the nominal working frequency
to the high frequency operation, and further optimize and adjust the power
supply and operation mode of the electric precipitator.
b) Energy Balanced FGD Technology
The power consumption of FGD facilities is reduced to less than 0.8% during
its rated operation by optimizing its system design and operation mode.
Applying a special heat recovery device, the heat in the flue gas and
the heat generated by the ID fan and the Booster fan during their operation
can be collected. The recovered heat can fully offset the power consumption
of the FGD facilities.
3. Energy Saving High Efficient Whole Day SCR Technology
To modify the turbine and thermal system, the extraction steam can be
increased during low load operation. This can relatively improve the feedwater
temperature in boiler low load and the flue gas temperature can be enhanced.
At the same time, to adjust the boiler heating surface, the catalyst can
run in the safe condition and high efficient area during the unit whole
load range.
4. Anti-Blocking and Anti-Corrosion Technology for Air Preheater
Expanding the philosophy of regeneration, to improve the intake air temperature
can remarkable lift the average operation temperature of the heating surface
in cold end of the air preheater. Thus the dewing area can be depressed
so that the dewing and clinging speed dropped. To ensure the flushing
by the flue gas larger than the clinging of the attachment, the blockage
of the air preheater can be avoided. At the same time, the corrosion can
be easily solved.
5. Safe, Energy saving, Lifetime Extending Technology of SCR Catalyst
Applying Feng’s brand new startup technology, except for the advantages
mentioned in Energy Saving, catalyst poisoned, carbon and ash deposited,
and catalyst sintered, hydrates formed on its surface will be avoided.
The operation lifetime of the catalyst can be extended greatly.
Advantage:
Feng’s series of environmental protection technologies cover de-dust, FGD
and SCR and can realize high efficient environmental protection based on
energy saving. These technologies have predominant advantages on both
economy and environment.
II. Reference in Waigaoqiao No.3 Power Plant
The emission is greatly reduced
Emission of dust: 11mg/m3
Emission of SO2: 60mg/m3
Emission of NOx ≤ 30mg/m
SCR efficiency≥89% (40%-100% load)
Preventing the corrosion and blockage of air preheater
Extending the lifetime of SCR catalyst
Fuel oil consumption in the Power Industry accounts for a large part of
the total fuel consumption, therefore, any oil-saving technology is of
great value. At present, the oil-saving technology in the US focuses on
the stable combustion at low load, whereas the oil-saving technology on
the stable combustion during start-up, outage or peak regulation is not
widely used. Note that oil consumption during start-up or outage of the
boiler takes about 60%, whereas low-load stable combustion takes about
40%.
Gasification small oil gun ignition and combustion techniques can be applied
in the combustion system of boilers in coal-fired power plants. The high
velocity flow breaks the fuel oil into fine jet sprays which atomize into
superfine oil mist and then combust. The heat generated by the combustion
rapidly heats the fuel and burns the oil mist, which allows the oil gun
to directly burn gasified fuel thus greatly improving the flame temperature
and thus burn efficiency. The temperature of the transparent flame core
can reach temperatures of 2750 deg F to 3650 deg F which directly ignites
coal dust which assists start up of the boilers under stable combustion
with low load.
With a low investment, small oil gun ignition technique saves oil for
the power stations by 90%, thereby reducing the cost of electricity generation.
This small oil gun ignition technique is applied widely in power stations
throughout China where the investment is re-paid after several outages.
Further, this small oil gun ignition and stable combustion technique saves
fuel oil and reduces the emissions of NOX and SOX.